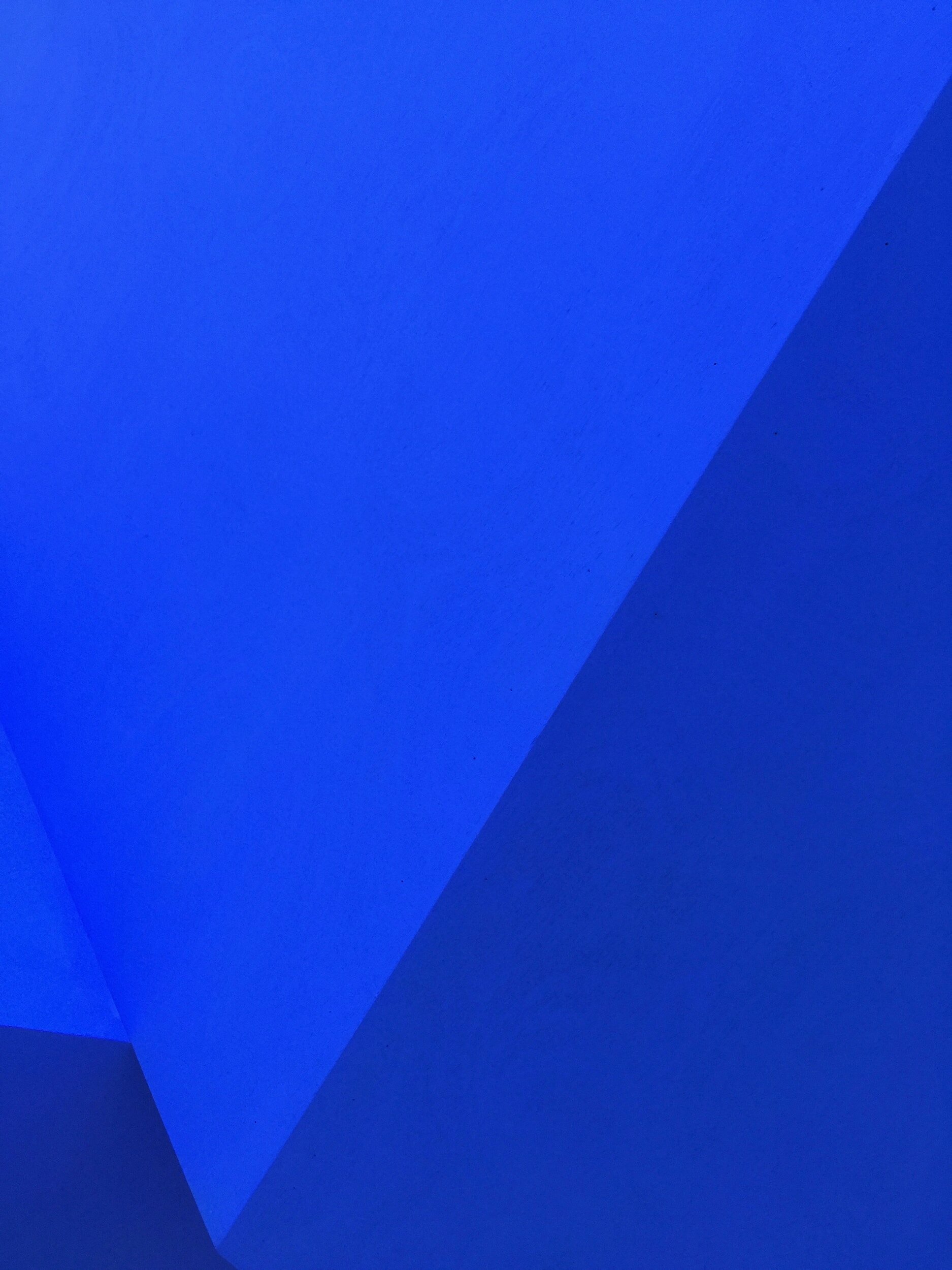
ULTRA™ Distillation Systems
ULTRA™ DS-10
10 gallons per hour (GPH)
Features
Distillation Capacity: 10 gallons/hour
Footprint: 38”Long x 39” Wide x 80” Tall
Typical electrical: 240V, 208 / 1 PH
NESHAP Compliant Distillation System
Automated continuous operation with ULTRA vapor degreaser
Increases solvent usage
Reduces vapor degreaser maintenance
Refrigerated—chiller not needed
Electric immersion heaters – 5,400 watts
ULTRA™ DS-20/DS-30
20 or 30 gallons per hour (GPH)
Features
Distillation Capacity: 20 or 30 gallons/hour
Footprint: 40”Long x 39” Wide x 80” Tall
Typical electrical: 240V, 208 or 460V/ 3 PH
If chiller cooled: requires 5 tons of capacity
NESHAP Compliant Distillation System
Automated continuous operation with ULTRA vapor degreaser
Increased solvent usage
Can be refrigerated or chiller cooled
Electric immersion heaters – 9,000 watts DS-20
Electric immersion heaters – 12,000 watts DS-30
ULTRA™ DS-60/DS-90
60 or 90 gallons per hour (GPH)
Features
Distillation Capacity: 60 or 90 gallons/hour
Footprint: 49”Long x 44” Wide x 81” Tall
Typical electrical: 240V, 208 or 460V/ 3 PH
If chiller cooled: requires 10 tons of capacity
NESHAP Compliant Distillation System
Automated continuous operation with ULTRA vapor degreaser
Increased solvent usage
Can be refrigerated or chiller cooled
Electric immersion heaters – 18,000 watts DS-60
Electric immersion heaters – 24,000 watts DS-90
Automated continuous operation with ULTRA™ Vapor Degreasers
Reduced solvent costs
Increased solvent usage
Elevated for easy solvent transfer to vapor degreaser or waste drum
Excellent solvent containment
Small footprint
Compatible with variety of solvents
120% freeboard
FEATURES | |
NESHAP Compliant Features | Yes |
120% freeboard | Yes |
Light Weight Lift-Off Lid | Yes |
High Volume Water Separator | Yes |
Primary Refrigeration | Copeland with Stainless Steel Coil |
Float System for Automated Operation | High & Low Level Float for Automatic Filling |
Watlow Safety Limit Controls | HTC -High Temp control LTC-Liquid Temp Control SVC-Safety Vapor Control WTC - Water Temp Control |
Overfill Safety Control | Yes |
Operator Lock-Out of Control | Yes |
Large Maintenance Clean Out Door | Yes |
Construction | 304 Stainless Steel |
Reduced Solvent Costs | Yes |
Increased Solvent Usage | Yes |
ULTRA™ Distillation System Features
Automated Continuous Operation - Solvent transfer pump activated by high and low level float for continuous automatic filling of the vapor degreaser.
Water or Chiller Cooled Primary Condensation Coil and Water Separator - Distillation system can be serviced by facility chilled water, public water supply or a re-circulating chiller.
High Volume Water Separator - High volume water separator. Sight-glass at discharge for viewing of solvent discharge flow and flow rate.
Float System for Automated Operation - High and low level float system for automatic filling of distillation system.
Low-Level Prevention - Low-level float and HTC control to ensure sufficient minimum solvent level for optimum operation.
WATLOW Safety Limit Controls - Safety controls display both set-point and actual temperature readings for each safety control providing efficient assessment of operating conditions in degreaser and easy diagnosis of safety failures.
Operator Lock-Out of Control Settings - Watlow controls allow for operator lock-out of changing of control setting.
Elevated Tank - Elevated distillation tank provides ease of tank interior maintenance and facilitates discharge of distillate directly in to solvent storage drum for batch operations.
Large Tank Maintenance Clean-Out Door
Easy Heating Element Maintenance - Elements are connected to the clean-out door instead of mounted to the bottom of the tank. Power is easily disconnected via plug from electrical control box.
Comprehensive 1-Year Manufacturer’s Warranty
Operator’s Manual
Simple Control Safety Panel
Primary Refrigeration Coils
Running Standard R134A Refrigerant
High Volume Water Separator
Distillation System Benefits
Seamlessly integrated operation with all ULTRA™ Vapor Degreasing Systems for continuous operation
Simple engineering and stoutness of design for durability and ease-of-maintenance
Excellent training including start-up, shut down, maintenance and good solvent cleaning work practices
Easy to support in the field with accessible heating elements, clear temperature read-outs, sophisticated indicator light system, and updated refrigeration systems using standard refrigerant
Cost effective operation and maintenance
Compact footprint
Effective with a variety of non-flammable solvents, including chlorinated, brominated and fluorinated
State-of-the-art engineering based on a best practices for simplicity, field supportability and reliability
Minimal Solvent Emissions and Reduced Operating Costs
Options
Optional upgrade to self priming pump for automated continuous operation
Optional power still bottom pump-out feature
Optional insulated tank walls with stainless steel sheathing
Optional distillation system filtration
Optional stainless steel spill containment tray
Choice of vapor degreasing solvent including EnTron™, EnTron™-Aero, GenTech™ and AeroTron™
Reliance Specialty Products, Inc.
The Only OEM Company That Manufactures Both Vapor Degreasing Equipment and Vapor Degreasing Solvent
Reliance Specialty Products, Inc. is known throughout the industry as vapor degreasing experts because we manufacture both the ULTRA™ vapor degreasing equipment line and AeroTron™ vapor degreasing solvents which are drop-in TCE and nPB replacement solvents.
ULTRA™ Vapor Degreaser FEATURES:
Minimize worker solvent exposure
Enhance solvent containment
Provide state of the art control systems
Allow easy field maintenance
Automate basket handling for consistent parts processing
Adept for the use of non-flammable solvents