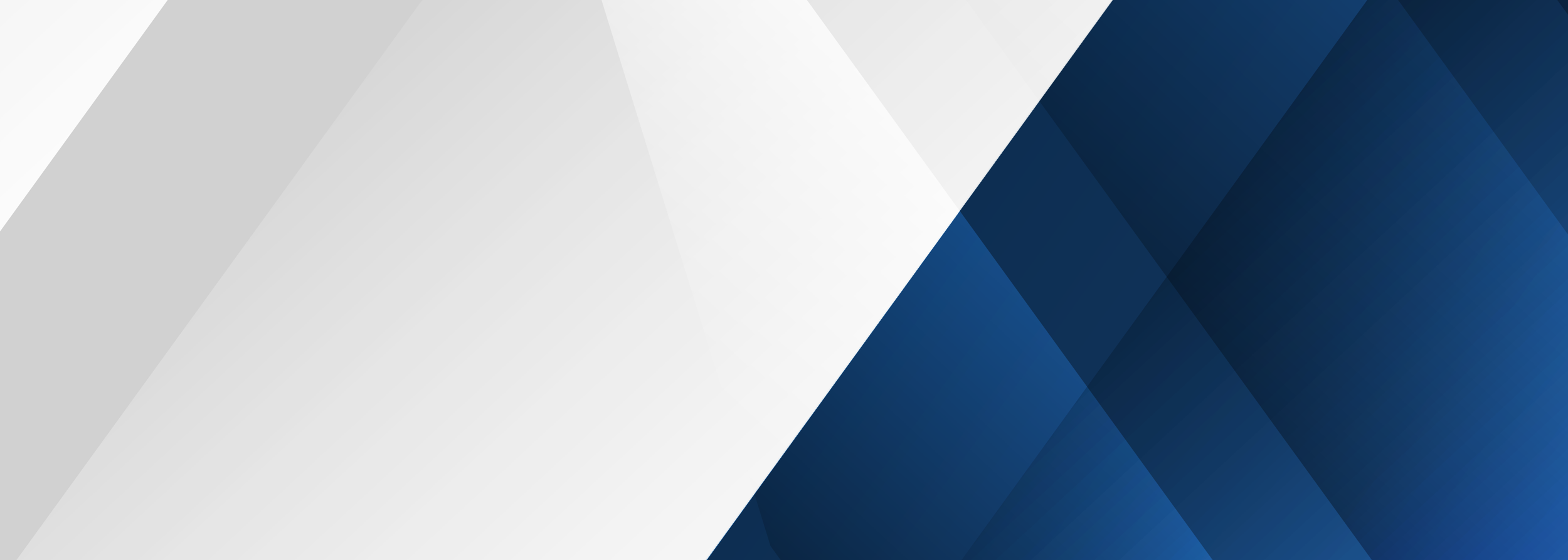
ULTRA MODEL 2012 LE
VAPOR DEGREASER
ULTRA™ Model 2012 LE Features:
Ultrasonic Immersion Sump - 20”L x 12”W x 12”D
Easy Maintenance
Spray Wand for Additional Cleaning
Excellent Solvent Containment and NESHAP Compliant
Reduced Solvent and Operating Costs
Small Foot-Print - available in narrow configuration to fit through 30” Door
On Casters for Mobility
Compatible with Variety of Solvents
120% Freeboard
CONTACT US TO LEARN MORE
Dual Basket Handling for Twice the Parts Processing
ULTRA™ 2012 LE Front with Lid Open
ULTRA™ 2012 LE Front View
ULTRA™ 2012 LE Top View
Easy Access Clean-Out Doors on Both Boil Side & Immersion Side
Tank Interior
Programmable Digital Controls
Stainless Steel Continuous Coil Primary & Secondary
ULTRA™ 2012 LE Rear View
ULTRA™ 2012 LE Side View
ULTRA™ 2012 LE Narrow (30" wide)
Basket Handling Elevator - Optional
Dual Automated Basket Handling Elevators - Optional
Biased Immersion / Ultrasonic Sump
Available in Narrow configuration which fits through a standard 30” door frame.
ULTRA™ 2012 LE Unit Specifications | |
---|---|
Dimensions | |
Ultrasonic Cleaning Tank | 20”L x 12”W x 12” Deep |
Vapor Cleaning Zone | 40”L x 12”W x 12” Deep |
Boil Tank | 20”L x 12”W |
Footprint Dimensions (without casters)** | 59”L x 55”W x 55” High** |
NARROW Footprint Dimensions | 80”L x 30”W x 47” High** |
Features | |
Ultrasonic Cleaning | 500 Watts of Power at 40 kHz Field replaceable components. Adjustable Power and Sweep. |
Vapor Cleaning | Vapor Cleaning Zone above Boil Tank and Ultrasonic Tank |
Spray Cleaning | Hand Spray Wand and Large Spray Reserve Tank |
Filtration of Ultrasonic Tank | Continuous Filtration |
Boil Tank Access Door | “Easy Ring” Door System |
Ultrasonic Tank Access Door | “Easy Ring” Door System |
Solvent Containment | |
NESHAP Compliant Features | Yes |
Primary Condensing Coil | Refrigerated Stainless Steel |
Low-Temp Freeboard Condensation Coil | Refrigerated Finned Stainless Steel operating at -10F to -20F |
Freeboard Ratio | 120% |
Horizontal Slide Lid | Manual or Automated |
Watlow Solvent Safety and Temperature Controls | HTC, LTC, SVC, VU, RT and Low-Level Float |
Monitoring of the Vapor Degreaser’s Correct Operating Condition | Comprehensive Indicator Light System and Temperature Displays |
Automated Part Cleaning | |
BHE Automated Basket Handling System | Yes—Optional |
Operating Requirements | |
Solvent Operating Requirement | 26 Gallons |
Typical Electrical Service | 208V or 240V / 1 Phase |
ULTRA™ 2012 LE Low Emission Features
Foot Activated Spray Lance System
NESHAP Compliant Vapor Degreasing System
Solid Stainless Steel Construction - Heavy gauge 304 stainless steel used on tank, water separator, spray reserve tank, primary coil, low-temperature coil, lid system, tank access doors and tank fittings.
Stainless Steel Primary Condensing Coil - New Copeland refrigeration system operating with standard R134A refrigerant.
Sub-Zero Temperature Condensing Coil - Finned stainless steel condensation coil with Copeland R404A refrigeration operating to approximately -20F thus broadening the height of the solvent flash-off dwell zone for enhanced solvent containment.
Foot Operated Spray Lance System - Mag-drive pump with distillate spray reservoir with Vapor Up Safety Control which requires presence of vapor to permit operation of spray wand.
High Volume Condensate Water Separator - feeding spray reservoir
Digital Display Safety Control Panel - including HTC, LTC, SVC, VU, RT
Ultrasonic Power – 500 Watts @ 40 kHz - field replaceable submersible transducers and plug in external ultrasonic generator for easy servicing
Ultrasonic Power - Input adjustment and sweep frequency adjustment
Ultrasonic Immersion Sump filtration and re-circulation system with mag-drive pump
WATLOW Temperature Safety Limit Controls - Digital display on control panel; temperature set point as well as actual temperature – SVC (Safety Vapor Control), HTC (High Temperature Control), LTC (Liquid Temperature Control) and RT (Refrigeration Temperature Control)
Low-Level Float Safety System - Ensures the minimum amount of solvent in boil sump for proper system operation.
Comprehensive Indicator Light System on Control Panel - Includes solvent low level float fault indicator lights (for easy identification of operating fault conditions). “Spray Ready” indicator light and zero coil “Defrost” indicator light, illuminated on/off switches for easy identification of system condition “Heat”, “Filtration”, Main Power”, “Refrigeration” and “Low-Temp Refrigeration”.
Horizontal Slide Lid - for solvent containment. Optional power roll-top available.
Casters - for easy movement.
Simple In and Out Electric Immersion Heater - “Screw-In” type elements for easy replacement.
Two Sump Access Clean-Out Doors - Boil sump and immersion sump access for ease of maintenance through the clean-out door rather than over the tank top
One (1) stainless steel workbasket
Comprehensive 1-Year Manufacturer’s Warranty
ULTRA™ 2012 LE Operator’s Manual
Primary and Sub-Zero Coils Running Standard Refrigerant
Simple Control Safety Panel
ULTRA™ 2012 LE Benefits
Simple engineering and stoutness of design for durability and ease-of-maintenance
Excellent training - start-up, shut down, maintenance and good solvent cleaning work practices
Easy to support in the field with accessible heating elements, clear temperature read-outs, sophisticated indicator light system, and updated refrigeration systems using standard refrigerant
Cost effective operation and maintenance
Compact footprint
Effective with a variety of non-flammable solvents, including chlorinated, brominated and fluorinated
State-of-the-art engineering based on a best practices for simplicity, field supportability and reliability
Minimal Solvent Emissions and Reduced Operating Costs due to NESHAP Compliant coils
Electrical Panel with Sophisticated Temperature Display and Indicator Light System
ULTRA™ 2012 LE Options
Electric horizontal slide lid
Additional baskets
Solvent Containment Spill Tray
Increased Ultrasonic Power
Choice of vapor degreasing solvent including EnTron™, EnTron-Aero™, GenTech™ and AeroTron™
Optional Vertical Basket Handling Elevator (BHE) for loads up to 35 lbs.
ULTRA™ 2012 LE: Compatible with Non-Flammable Solvents
Simple Change over - The ULTRA™ 2012 LE is engineered to be compatible with a variety of solvents and in most cases a simple clean out and change of temperature settings is all that is required.
120% Freeboard — helps with vapor containment - so using chlorinated solvents like TCE, TCA, MCL and PERC is still possible.
Sub-Zero refrigeration coil - in addition to the primary refrigeration system, makes using brominated solvents like GenTech™, EnTron™ and EnTron-Aero™ or Modernized chemistries solvents such as AeroTron - an economical alternative.
Manual or Automated Slide-Lid - provides additional solvent containment for the new generation of fluorinated solvents like AeroTron™ and helps reduce evaporation.
Reliance Specialty Products' core business is vapor degreasing solvent cleaning. We research, develop, manufacture, and expertly support advanced solvent cleaning products and metal finishing products.
We manufacture vapor degreasing solvents and low-emission NESHAP Compliant vapor degreasing equipment that provide years of quality, reliability and productivity.
Ready to Help Responsive Reliable
We are leaders in Comprehensive Vapor Degreasing Training, Maintenance and Solvent Cleaning Work Practices