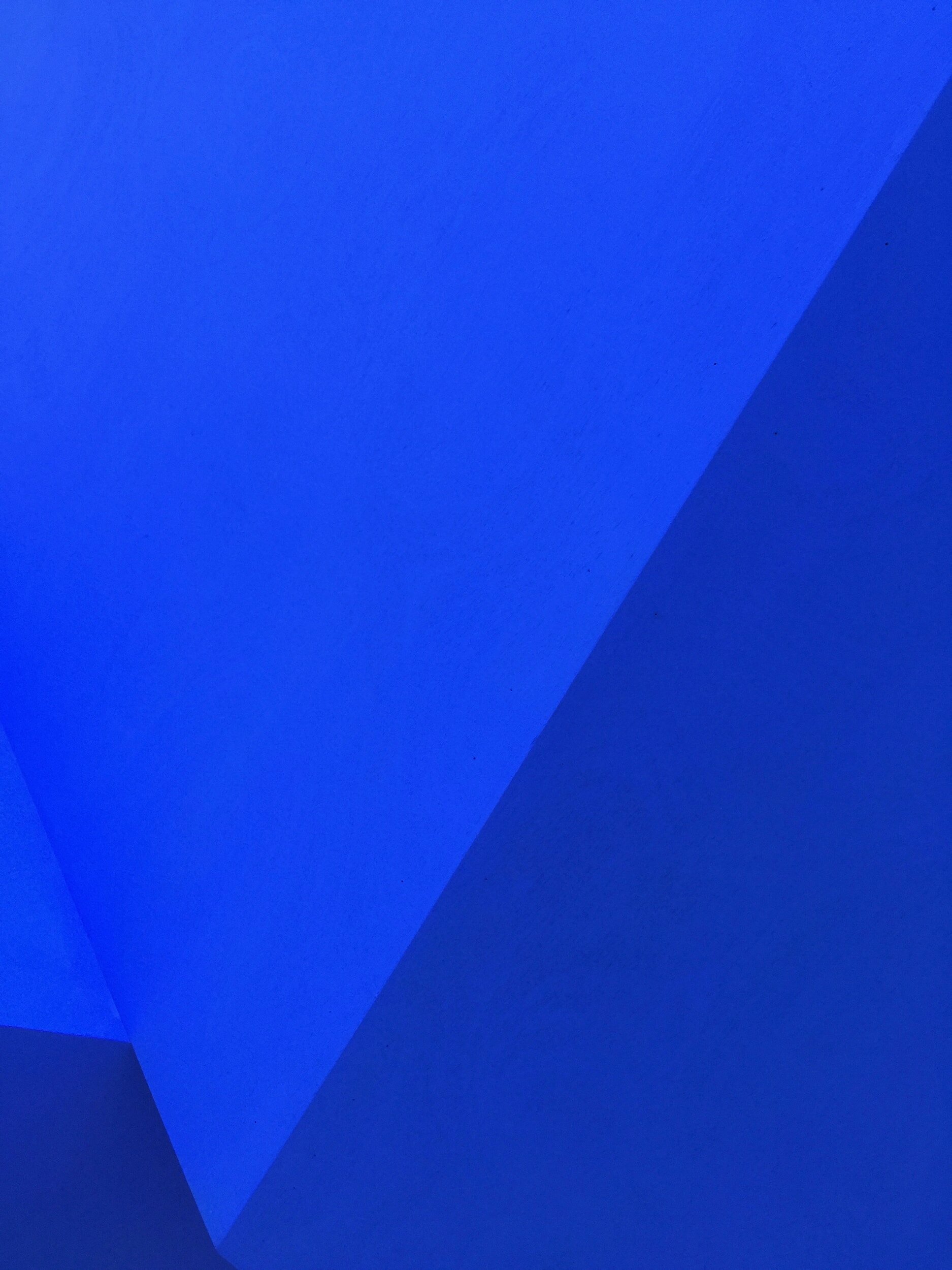
Ultra Model 2012-Narrow Vapor Degreaser
ULTRA™ Model 2012-Narrow Low Emission Features:
High Performance Cleaning
Fits Through a Standard 30” Door!
Ultrasonic Immersion Sump - 20”L x 12”W x 12”Deep
Easy Maintenance
Spray Wand for Additional Cleaning
Excellent Solvent Containment and NESHAP Compliant
Reduced Solvent and Operating Costs
Small Foot-Print
On Casters for Mobility
Compatible with Variety of Solvents
120% Freeboard
ULTRA™ 2012 LE-N - Tank View
ULTRA™ 2012 LE-N - Front of Tank
ULTRA™ 2012 LE-N - Left Side
ULTRA™ 2012 LE-N - Left Side View, Panel Open
ULTRA™ 2012 LE-N - Right Side
ULTRA™ 2012 LE-N - Top of Tank
ULTRA™ 2012 LE-N - Back of Tank
ULTRA™ 2012 LE-N - Easy Read Temp Controls
ULTRA™ 2012 LE-N - Clean Out Doors
ULTRA™ 2012 LE-N - Heating Elements
ULTRA™ 2012 LE-N - Tank Interior
ULTRA™ 2012 LE-N - Primary & Secondary Refrigeration Coils
ULTRA™ 2012 LE-N - Filtration with Gauge
ULTRA™ 2012 LE-N - Ultrasonics up to 1000W
ULTRA™ 2012 LE-N - Power Pump Out
AeroTron™ Solvent
ULTRA™ 2012-N LE Unit Specifications | |
---|---|
Dimensions | |
Ultrasonic Cleaning Tank | 20”L x 12”W x 15” Deep |
Vapor Cleaning Zone | 40”L x 12”W x 12” Deep |
Boil Tank | 20”L x 12”W |
Footprint Dimensions (without casters) | 84”L x 30”W x 47” High |
Features | |
Ultrasonic Cleaning | 500 or 1000 Watts of Power at 40 kHz. Field replaceable components. Adjustable Power and Sweep. |
Vapor Cleaning | Vapor Cleaning Zone above Boil Tank and Ultrasonic Tank |
Spray Cleaning | Hand Spray Wand and Large Spray Reserve Tank |
Filtration of Ultrasonic Tank | Continuous Filtration |
Boil Tank Access Door | “Easy Ring” Door System |
Ultrasonic Tank Access Door | “Easy Ring” Door System |
Solvent Containment | |
NESHAP Compliant Features | Yes |
Primary Condensing Coil | Refrigerated Stainless Steel |
Low-Temp Freeboard Condensation Coil | Refrigerated Finned Stainless Steel operating at -10F to -20F |
Freeboard Ratio | 120% |
Horizontal Slide Lid | Manual or Automated |
Watlow Solvent Safety and Temperature Controls | HTC, LTC, SVC, VU, RT and Low-Level Float |
Monitoring of the Vapor Degreaser’s Correct Operating Condition | Comprehensive Indicator Light System and Temperature Displays |
Automated Part Cleaning | |
BHE Automated Basket Handling System | Yes—Optional |
Operating Requirements | |
Solvent Operating Requirement | 26 Gallons |
Typical Electrical Service | 208V or 240V / 1 Phase |
ULTRA™ 2012-N LE Low Emission Features
Foot Activated Spray Lance System
NESHAP Compliant Vapor Degreasing System
Fits Through Standard 30” Door
Solid Stainless Steel Construction - Heavy gauge 304 stainless steel used on tank, water separator, spray reserve tank, primary coil, low-temperature coil, lid system, tank access doors and tank fittings.
Stainless Steel Primary Condensing Coil - New Copeland refrigeration system operating with standard R134A refrigerant.
Sub-Zero Temperature Condensing Coil - Finned stainless steel condensation coil with Copeland R404A refrigeration operating to approximately -20F thus broadening the height of the solvent flash-off dwell zone for enhanced solvent containment.
Foot Operated Spray Lance System - Mag-drive pump with distillate spray reservoir with Vapor Up Safety Control which requires presence of vapor to permit operation of spray wand.
High Volume Condensate Water Separator - feeding spray reservoir
Digital Display Safety Control Panel - including HTC, LTC, SVC, VU, RT
Ultrasonic Power – 500 Watts @ 40 kHz - field replaceable submersible transducers and plug in external ultrasonic generator for easy servicing
Ultrasonic Power - Input adjustment and sweep frequency adjustment
Ultrasonic Immersion Sump filtration and re-circulation system with mag-drive pump
WATLOW Temperature Safety Limit Controls - Digital display on control panel; temperature set point as well as actual temperature – SVC (Safety Vapor Control), HTC (High Temperature Control), LTC (Liquid Temperature Control) and RT (Refrigeration Temperature Control)
Low-Level Float Safety System - Ensures the minimum amount of solvent in boil sump for proper system operation.
Comprehensive Indicator Light System on Control Panel - Includes solvent low level float fault indicator lights (for easy identification of operating fault conditions). “Spray Ready” indicator light and zero coil “Defrost” indicator light, illuminated on/off switches for easy identification of system condition “Heat”, “Filtration”, Main Power”, “Refrigeration” and “Low-Temp Refrigeration”.
Horizontal Slide Lid - for solvent containment. Optional power roll-top available.
Casters - for easy movement.
Simple In and Out Electric Immersion Heater - “Screw-In” type elements for easy replacement.
Two Sump Access Clean-Out Doors - Boil sump and immersion sump access for ease of maintenance through the clean-out door rather than over the tank top
One (1) stainless steel workbasket
Comprehensive 1-Year Manufacturer’s Warranty
ULTRA™ 2012 LE-N Operator’s Manual
Primary and Sub-Zero Coils Running Standard Refrigerant
Simple Control Safety Panel
ULTRA™ 2012-Narrow Low Emission Benefits
Simple engineering and stoutness of design for durability and ease-of-maintenance
Excellent training - start-up, shut down, maintenance and good solvent cleaning work practices
Easy to support in the field with accessible heating elements, clear temperature read-outs, sophisticated indicator light system, and updated refrigeration systems using standard refrigerant
Cost effective operation and maintenance
Compact footprint fits through standard doorway
Effective with a variety of non-flammable solvents, including chlorinated, brominated and fluorinated
State-of-the-art engineering based on a best practices for simplicity, field supportability and reliability
Minimal Solvent Emissions and Reduced Operating Costs due to NESHAP Compliant coils
Electrical panel with sophisticated temperature display and indicator light system
ULTRA™ 2012-N LE Options
Electric horizontal slide lid
Additional baskets
Solvent Containment Spill Tray
Increased Ultrasonic Power
Choice of vapor degreasing solvent including AeroTron™, EnTron™, EnTron-Aero™, and GenTech™
Optional Vertical Basket Handling Elevator (BHE) for loads up to 35 lbs.
ULTRA™ 2012-N LE: Compatible with Non-Flammable Solvents
Simple Change over - The ULTRA™ 2012-Narrow Low Emission unit is engineered to be compatible with a variety of solvents and in most cases a simple clean out and change of temperature settings is all that is required.
120% Freeboard — helps with vapor containment - so using chlorinated solvents like TCE, TCA, Methylene Chloride and PERC is still possible.
Sub-Zero refrigeration coil - in addition to the primary refrigeration system, makes using brominated solvents like GenTech™, EnTron™ and EnTron-Aero™ or Modernized chemistries solvents such as AeroTron - an economical alternative.
Manual or Automated Slide-Lid - provides additional solvent containment for the new generation of fluorinated solvents like AeroTron™ and helps reduce evaporation.
Reliance Specialty Products' core business is vapor degreasing solvent cleaning. We research, develop, manufacture, and expertly support advanced solvent cleaning products and metal finishing products.
We manufacture vapor degreasing solvents and low-emission NESHAP Compliant vapor degreasing equipment that provide years of quality, reliability and productivity.
Ready to Help Responsive Reliable
We are leaders in Comprehensive Vapor Degreasing Training, Maintenance and Solvent Cleaning Work Practices