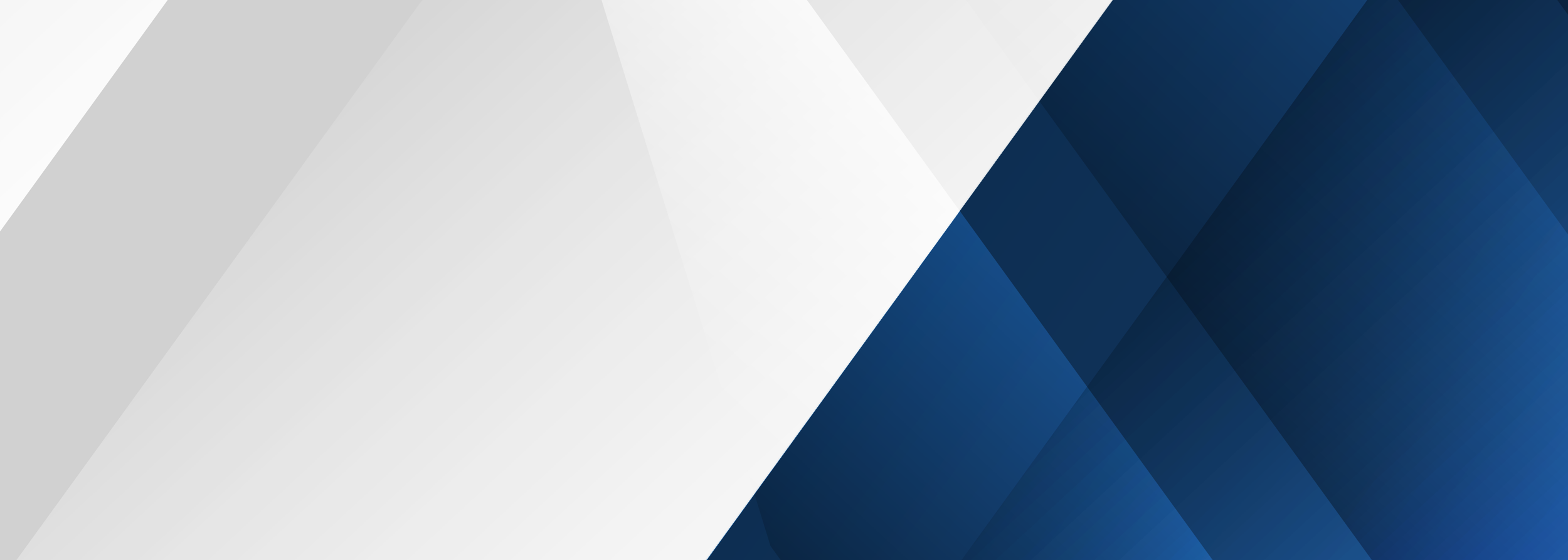
HOW DOES A
VAPOR DEGREASER WORK?
What Is a Vapor Degreaser?
A vapor degreaser is a cleaning system (also known as a parts washer) that boils non-flammable solvent to the point the solvent turns to vapor and the vapor dissolves the oil/grease or other containment to clean the metal, optical, or PCB part.
There are four key interior parts to the vapor degreaser:
The Boil Chamber - where the solvent is heated to boiling
The Vapor Zone - where the initial part cleaning takes place
The Immersion Chamber - where parts can be immersed in clean solvent and ultrasonics applied for additional cleaning
The Refrigerated Containment Zone - where the parts are cooled and dried; the refrigeration zone cools the solvent so it does not escape from the tank
1. The Boil Chamber
Heating elements boil the liquid solvent to create large amounts of solvent vapor. The vapor generated from the boil chamber creates a solvent rich vapor zone for cleaning the parts. (Click anywhere on an image to enlarge it.)
2. The Vapor Zone
Vapor cleaning can be conducted anywhere in the vapor zone. Unique to a vapor degreaser system, large amounts of clean vapor are generated perpetually for vapor cleaning.
Vapor cleaning occurs when the vapor condenses on the part - in the vapor zone. The chemical properties of the solvent dissolve the oils, greases and other solvent soluble contaminants and they are flushed off the part by the continuous condensation flow of the solvent off the part.
The solvent takes the contaminant (like oil) into solution and drops back into the tank where it is filtered and cleaned for reuse. So a typical degreaser is not only a cleaning system, it also acts as a distillation system to recycle the solvent for continued use. (Click anywhere on an image to enlarge it.)
3. The Immersion Chamber
The immersion chamber is used for immersion and ultrasonic cleaning. Parts baskets can be immersed and ultrasonics applied to ensure parts with blind holes and complex geometries are cleaned completely. The benefit vapor degreasing solvents is that they have a high surface tension and this helps the solvent penetrate areas that often get missed by water (which has a low surface tension) and other cleaning modalities.
The physical movement of solvent over the surface of the part, either by dipping or multi-dipping, flushes the contaminant and other non-soluble soils from the surface of the part.
Ultrasonic cavitation (an optional feature) on the surface of the parts while the parts are submerged in the ultrasonic immersion tank enhances the cleaning via an implosion of ultrasonic cavitation bubbles - which creates a strong mechanical action on the wetted surface of the parts to separate the non-soluble solvent soils from the part surface.
Another benefit of vapor degreasers is that the immersion chamber is always filled with clean distillate - so contaminants are not redeposited back on the part - as might happen with traditional aqueous, ultrasonic baths.
Note: Vapor Degreasers with an immersion/ultrasonic chamber are considered 2-tank systems because you have a boil or "dirty" side where the dirt accumulates for distillation and you have an immersion (ultrasonic) side for additional part cleaning.
Traditional vapor degreasers (and large units) typically have only a "Vapor Zone" with no immersion capabilities. (Click anywhere on the image to enlarge it.)
4. The Refrigeration Containment Zone
The refrigeration zone consists of a primary refrigeration coil which is cooled to 45°F (7°C) and a "sub-zero" refrigerated coil -20°F (-29°C) that creates a blanket of cool air over the vapor zone to contain the solvent and reduce solvent loss and emissions.
As the part basket is moved into the refrigeration zone, the parts are dried as the solvent is cooled and drips back into the tank. The parts are now completely clean and dry - in a matter of seconds.
Therefore, the refrigeration containment zone not only ensures solvent containment, thus reducing emissions and minimizing solvent loss, but also helps to dry and cool the parts making them ready for the next manufacturing stage such as adhesion or painting. (Click anywhere on an image to enlarge it.)
ROI of a Vapor Degreaser is Significant
In general, vapor degreasing is a powerful, efficient way to clean lots of part fast. Between the increased cleaning efficiency, reduced processing time, increased throughput and eliminated post processing, the return on investment of a vapor degreasing system is significant. Contact us or give us a call 847.640.8923 to learn more.