Is Vapor Degreasing Right For You?
Understanding the Key Benefits of Parts Cleaning with Vapor Degreasing
Part cleaning is an important step of any manufacturing process. Reducing the amount of time spent cleaning while increasing the overall quality of cleaning are two of the great benefits of vapor degreasing.
Part cleaning is an important step of any manufacturing process. And ensuring part cleanliness requirements are met is vital. However, part cleaning can be tedious and time consuming. Reducing the amount of time spent cleaning while increasing the overall quality of cleaning is one of the great benefits of vapor degreasing. In this summary, we will review the reasons many manufacturers use vapor degreasing to help you see if vapor degreasing will benefit your company as well.
Benefit 1: Increased Cleanliness
Question: Are my parts getting clean enough? Am I having adhesion, plating or other issues present because of cleanliness issues? If the answer is yes, vapor degreasing should be considered.
Consistent and comprehensive part cleanliness is one of the major reasons companies choose vapor degreasing. It is an effective cleaning process for removing lubricants, greases, waxes, oils, and other machining contaminants introduced in the manufacturing process. The vapor degreasing process pulls the soil from the part, while not introducing any new contaminants (like detergents or surfactants). The cleaning is comprehensive as every surface is equally impacted by the solvent.
Benefit 2: Increased Throughput
Question: Do I need to clean and process more parts than my current cleaning process can handle? If I need more parts cleaned faster, vapor degreasing could be a good option.
Vapor degreasing is an efficient, effective way to clean many parts fast. And there is the added benefit of not needing to wipe or dry any residue from the parts after cleaning. The parts are ready for plating or whatever the next manufacturing step is. Vapor degreasing is fast, and in many cases can reduce cleaning processing times by 50% to 90% over hand wiping or aqueous cleaning systems. Increased throughput & reduced processing time.
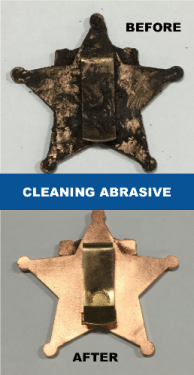
Cleaning Abrasive from Metal Badges
These badges are covered, front and back, with polishing abrasive. Vapor degreasing outfitted with ultrasonics completely cleans the badge in less than 5 minutes. No scrubbing, drying or rinsing necessary.
Benefit 3: Cost Savings
Question: Are the costs of our cleaning operation reducing overall profitability? Is the cleaning process of our business an issue? Is our cleaning process a bottleneck, slowing down the manufacturing throughput? If so, vapor degreasing can increase profitability substantially.
In general, the return on investment (ROI) of a vapor degreaser is excellent. The increased productivity, enhanced part cleaning consistency, and increased worker safety combined with reduced maintenance and labor can deliver significant cost savings.
Benefit 4: Consistent Cleaning
Question: Is "quality" suffering? Or are there increased costs incurred by part-rejection because of inconsistent cleaning? Do parts need to be cleaned to a military or cleaning specification - consistently? If so, vapor degreasing can be an excellent remedy.
For many companies, consistency of part cleaning is an issue. Some parts are cleaned well, others are rejected because of soils left after hand wiping, dipping or other cleaning method. All parts have a cost tied to them. If a part is rejected due to poor cleaning, the part either must be re-cleaned or scrapped, which adds cost and affects the bottom line.
Consistency of cleaning is a hallmark of vapor degreasing as it provides a complete enveloping of solvent around the part to clean it. Even blind-holes and complex geometries are effectively cleaned with vapor degreasing. Vapor degreasing provides the ability to clean thousands of parts with clean distilled solvent - over and over.
Additionally, automation via a basket handling system, or hoist provides cleaning "recipes" that ensure every part is cleaned to the same specification repeatedly and consistently. Automated hoists eliminate operator error while increasing processing efficiency.
Benefit 5: Increased Worker Safety
Question: Is worker safety a significant consideration? Is a reduction in emissions and worker exposure of primary importance? If so, vapor degreasing will provide an excellent combination of safety for workers with increased productivity.
Overall vapor degreasing systems limit worker exposure to solvents while reducing manual labor. With the addition of automation as discussed above, worker stress and strain while cleaning parts can be reduced significantly.
Benefit 6: Reduced Maintenance
Question: Am I spending more time and money maintaining cleaning equipment then getting the production needed? Vapor degreasing is a smart option for simplifying part cleaning.
Reliance ULTRA™ vapor degreasers are smartly designed systems that efficiently clean parts with minimal maintenance. They have exceptionally long life-span to give you years of consistent part cleaning.
Conclusion
The return on investment of a vapor degreasing system can be significant. Reliance ULTRA™ vapor degreasers are smartly designed systems that efficiently clean parts – fast. Once the initial investment is made, years of consistent cleaning can be achieved. The long-term savings of increased consistent cleanliness, reduced processing time, while cleaning more parts make vapor degreasing the right parts cleaning option for many companies in a variety of industries from aerospace to electronics to metal fabrication.
_______________________________________
Give us a call or contact us to discuss your application and how vapor degreasing might be an option for you. We can test clean parts in a vapor degreaser and share our recommendations for optimized cleaning.
At Reliance, we take a comprehensive, systemic approach to supporting our customers to finding solution to their cleaning needs. Reliance Technical Support Department at 847-640-8923. We are glad to be of assistance.