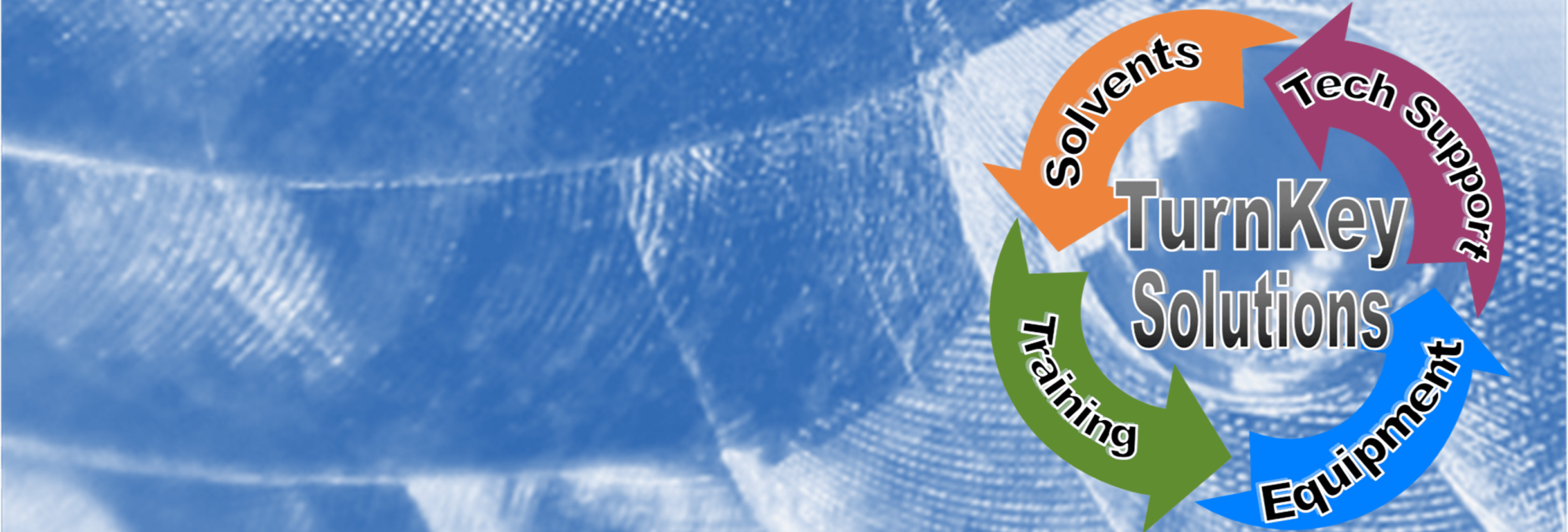
The Benefits of Vapor Degreasing
Introduction
Consistent part cleanliness is one of the major reasons many companies choose vapor degreasing. This video provides an overview of the key benefits of vapor degreasing.
Read about the benefits below…
BENEFIT: Increased Part Cleanliness
Consideration:
Are my parts getting clean enough? Am I having adhesion, plating or other issues present because of cleanliness issues?
If the answer is yes, vapor degreasing should be considered.
Consistent part cleanliness is one of the major reasons companies choose vapor degreasing.
During manufacturing, machined parts may become contaminated or soiled in production. Therefore, removing contaminants before moving to the next stage of the manufacturing process is critical.
When parts cannot be adequately cleaned with cold wiping, a heated approach may be needed.
Vapor degreasing is an effective cleaning process used for contaminant removal at many stages of the manufacturing process. Parts are cleaned in heated vapor alone and with ultrasonic immersion if needed.
Because precision cleaning applications require the complete removal of contaminants while ensuring that new contaminants are not introduced in the process, vapor degreasing is an excellent choice. The vapor degreasing process helps to pull the soil from the part, while not introducing any new contaminants.
Vapor degreasing increases the speed at which parts are cleaned and increases the cleanliness of the parts cleaned.
BENEFIT: Increased Throughput
Consideration:
Do I need to clean and process more parts than my current cleaning process can handle? If I need more parts cleaned faster, vapor degreasing could be a good option.
Vapor degreasing is an efficient, effective way to clean many parts fast. And there is the added benefit of not needing to wipe or dry any residue from the parts after cleaning. The parts are ready for plating or whatever the next manufacturing step is.
Vapor degreasing is fast and in many cases can reduce cleaning processing times by 50% to 90% over hand wiping or aqueous cleaning systems.
BENEFIT: Consistent Cleaning
Consideration:
Is "quality" suffering? Or are there increased costs incurred by part-rejection because of inconsistent cleaning? Do parts need to be cleaned to a military or cleaning specification - consistently?
If so, vapor degreasing can be an excellent remedy.
For many companies, consistency of part cleaning is an issue. Some parts are cleaned well, others are rejected because of soils left after hand wiping, dipping or other cleaning method.
All parts have a cost tied to them. If a part is rejected due to poor cleaning, the part either must be re-cleaned or scrapped, which adds cost and affects the bottom line.
Consistency of cleaning is a hallmark of vapor degreasing as it provides a complete enveloping of solvent around the part to clean it. Even blind-holes and complex geometries are effectively cleaned with vapor degreasing.
Vapor degreasing provides the ability to clean thousands of parts with clean distilled solvent - over and over.
Additionally, automation via a basket handling system, or hoist provides cleaning "recipes" that ensure every part is cleaned to the same specification repeatedly and consistently.
Automated hoists eliminate operator error while increasing processing efficiency.
BENEFIT: Worker Safety
Consideration:
Is worker safety a significant consideration? Is a reduction in emissions and worker exposure of primary importance?
If so, vapor degreasing will provide an excellent combination of safety for workers with increased productivity.
To reduce solvent emissions, vapor degreasers have two sets of refrigeration coils inside of the unit. The chilled coils create a stationary, cool air zone above the vapor zone that contains the vapor within the tank - keeping the vapor from escaping into the air. The cool air of the refrigeration zone presses down on the warm air of the vapor zone to keep it contained in the degreaser.
Vapor degreasing solvents are non-flammable and exceptional at removing hydrocarbons and other contaminants like grease and machining oils. The next generation of vapor degreasing solvents are considered non-hazardous and safer than older solvents.
BENEFIT: Reduced Maintenance
Consideration:
Am I spending more time and money maintaining cleaning equipment then getting the production needed?
Vapor degreasing is a smart option for simplifying part cleaning.
ULTRA™ vapor degreasers are smartly designed systems that efficiently clean parts with minimal maintenance.
BENEFIT: Cost Savings
Consideration:
Are the costs of our cleaning operation reducing overall profitability? Is the cleaning process of our business an issue? Is our cleaning process a bottleneck, slowing down the manufacturing throughput?
If so, vapor degreasing can increase profitability substantially.
Inconsistent cleanliness, outdated equipment, insufficient throughput, excessive downtime and maintenance can increase costs fast. In general, the return on investment (ROI) of a vapor degreaser is excellent. The increased productivity, enhanced part cleaning consistency, and increased worker safety combined with reduced maintenance and labor can deliver significant cost savings.
Conclusion
The return on investment of a vapor degreaser can be significant. Once the initial investment is made, years of consistent cleaning can be achieved. The long-term savings of increased consistent cleanliness, reduced processing time, while cleaning more parts make vapor degreasing the right cleaning solution.
Give us a call at 847.640.8923 and let our vapor degreasing experts help you optimize your part cleaning.