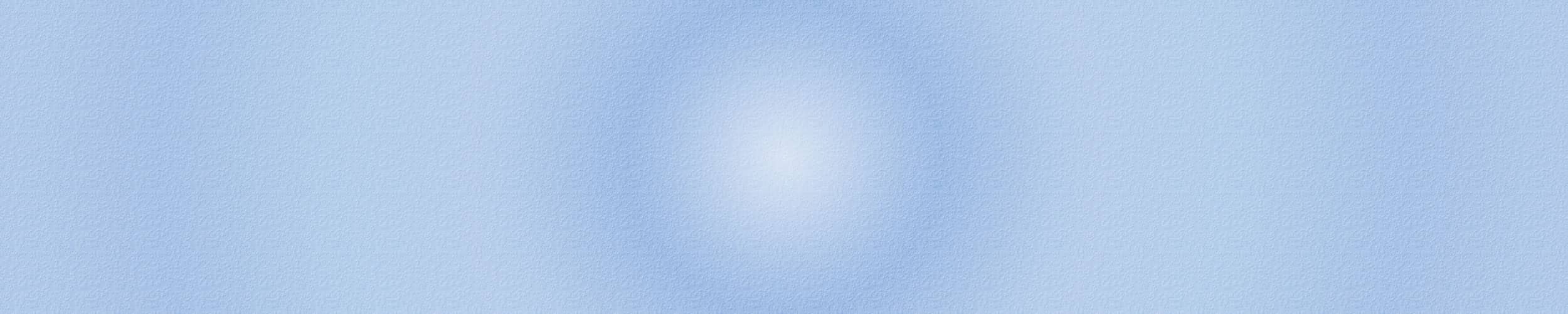
Ultrasonic Cleaning in a Vapor Degreaser
Cleaning with ultrasonics offers several advantages over conventional vapor degreasing. An overview of how ultrasonics work, and its advantages as well as the different ultrasonic equipment available will be the focus of this technical overview.
It has been our experience that the addition of an ultrasonic immersion step to the cleaning process used in an existing vapor degreasing system has proven to be very effective at enhancing the cleaning performance of solvent cleaning agents used in that system. We would recommend that, before changing solvent cleaning agents, or purchasing new equipment, any company experiencing cleaning performance issues of cleanliness, through-put or consistency in their vapor degreasing system should fully explore whether the mechanical surface cleaning achieved by ultrasonics cavitation (the rapid buildup and collapse of numerous minute bubbles on your parts' surface) can resolve those cleaning issues.
Ultrasonic Equipment and How Ultrasonics Clean
The three main components of ultrasonic cleaning are the ultrasonic transducers, an ultrasonic generator, and suitable ultrasonic power controls. The ultrasonic generators convert electrical energy, typically 50Hz or 60Hz, to the high frequencies used in ultrasonics, typically 20 to 120 kHz. The generator supplies this high frequency energy to the transducers which convert this power into mechanical vibrations. These mechanical vibrations form micron sized bubbles ( 1 micron = 1/1,000,000 of a meter) that implode in a process called "cavitation". It is estimated that a pressure of more than 10,000 psi and a temperature greater than 10,000°F can exist within the imploding cavitation bubble. The energy and cleaning effect of one bubble is incidental, however, the cumulative effect of the formation and collapse of millions of these bubbles per second is a very intense and effective mechanical cleaning action on the surface of the parts.
The frequency of the transducer determines the size of the bubble and the energy released. The lower frequencies create larger bubbles and more energy. Higher frequencies have less energy and are typically used for smaller, more delicate parts where damage to the part may be a problem or where the geometries are complex or the contaminant of an extremely fine nature. The effect of millions of tiny implosions in a solvent tank releases energy that can penetrate deep into blind holes and crevices of parts, physically removing bonded contaminants and increasing cleaning action.
There are two types of transducers currently used in ultrasonics: Piezoelectric and Magnetostrictive. Both convert electrical energy to mechanical energy, but magnetostrictive transducers typically operate at frequencies below 20 kHz whereas piezoelectric transducers can operate up to 120 kHz. Magnetostrictive transducers are typically more expensive and are known for their consistency and durability. Piezoelectric transducers are widely used because their components are relatively inexpensive; however these transducers can deteriorate over time effecting the frequency and power of the transducer and consequently its cleaning performance.
The Advantage of Ultrasonics
Solvent cleaning in a vapor degreaser before the invention of ultrasonics relied almost exclusively on the solvency power of the cleaning agents. There, of course, was the rinsing power of the vapor condensing on the part and the mechanical rinsing of the spray wand. But for the most part, these steps have only limited effectiveness compared to what can be achieved with ultrasonics.
Ultrasonic cleaning in your vapor degreaser should strongly be considered if you have any of these following conditions or concerns:
Contaminants containing inorganic contaminants such as salts, metal fines, buffing compounds or the inorganic components of a flux resin)
Contaminants that are baked on or cured or have difficulty being solublized by your cleaning agent, and
Parts that have complex geometries, blind holes or crevices.
By introducing ultrasonics into the vapor degreasing process, the capability of the system to clean in the previously mentioned contexts is dramatically improved. At a micro level, intense activity on the surface of the parts is possible to physically displace and dislodge hard to remove insoluble contaminants as well as reach blind holes, threads and cavities that conventional solvent vapor degreaser cleaning would have difficulty reaching and cleaning. In addition, in many instances the rate at which organic contaminants are cleaned is accelerated by the ultrasonic process.
Upgrading Your Vapor Degreasing System to Include Ultrasonic Cleaning
The simplest and most cost effective option for adding ultrasonics to your existing cleaning process is to retrofit you system with modular immersible transducers. For may existing vapor degreasing users this is a very attractive option because it avoids significant expense and effort to mount the transducers to the immersion tank which is very time and labor intensive. In addition, immersible transducers permit easy access for maintenance and inspection as well as quick and easy change out in the event that the transducers need to be repaired or replaced.
The size, frequency, type, and necessary wattage of the transducer depends on the tank size, the cleaning load and the cleaning agent's threshold of cavitation. Immersible transducers are available in kHz ranging from 25 to 170 kHz and from between 600 and 1500 watts for a single transducer module. More complicated units employing sweep and multiple frequency modulations are also available for module transducer units. The transducers are mounted either on the side of the tank or the bottom depending on the application and tank geometry. The ultrasonic generator can be mounted on the equipment or remotely mounted and an ultrasonic power control that permits the power to be adjusted is a feature we recommend to permit the refinement of the performance of the ultrasonics process to different work loads, a variety of parts and the part's sensitivity to the ultrasonics process.
Practical Considerations and Caveats
Fully exposing your parts to the cleaning solvent and to the ultrasonic action is of paramount importance to achieving effective cleaning. Your racking system and cleaning process must ensure that the parts are fully flooded with solvent. There should be no opportunity for air pockets in crevices or blind holes to form because there will be no solvent or ultrasonic cleaning in those areas. Racking of parts with some space in-between is optimal. However, in many instances, racking is not possible; in such cases, rotation of the parts to facilitate rinsing and elimination of air pockets is often a worthwhile procedure.
A proper balance of energy to work load and tank size needs to be achieved in your ultrasonic system. If you have too little wattage as compared to the tank size or the surface area of the parts being cleaned, then the ability of the ultrasonics to perform will be diminished. If you have too much wattage, then there is a possibility, especially with soft substrates, that the parts will become etched or damaged by the ultrasonics. As mentioned previously, an ultrasonic power controller allows the tailoring of the power to multiple variables.
Re-disposition of contaminants must also be avoided by properly maintaining your solvent bath and by properly designed racking and work procedures.
A final caveat is that trial testing is strongly recommended, particularly on inherently fragile parts such as printed circuit boards, to ensure that the ultrasonic process you have chosen is not damaging the parts. There are many variables involved in ultrasonic cleaning and many decisions to be made. Our technical staff would be pleased to help by providing guidance or running test parts in one of our test units at our facility under a number of different cleaning parameters.