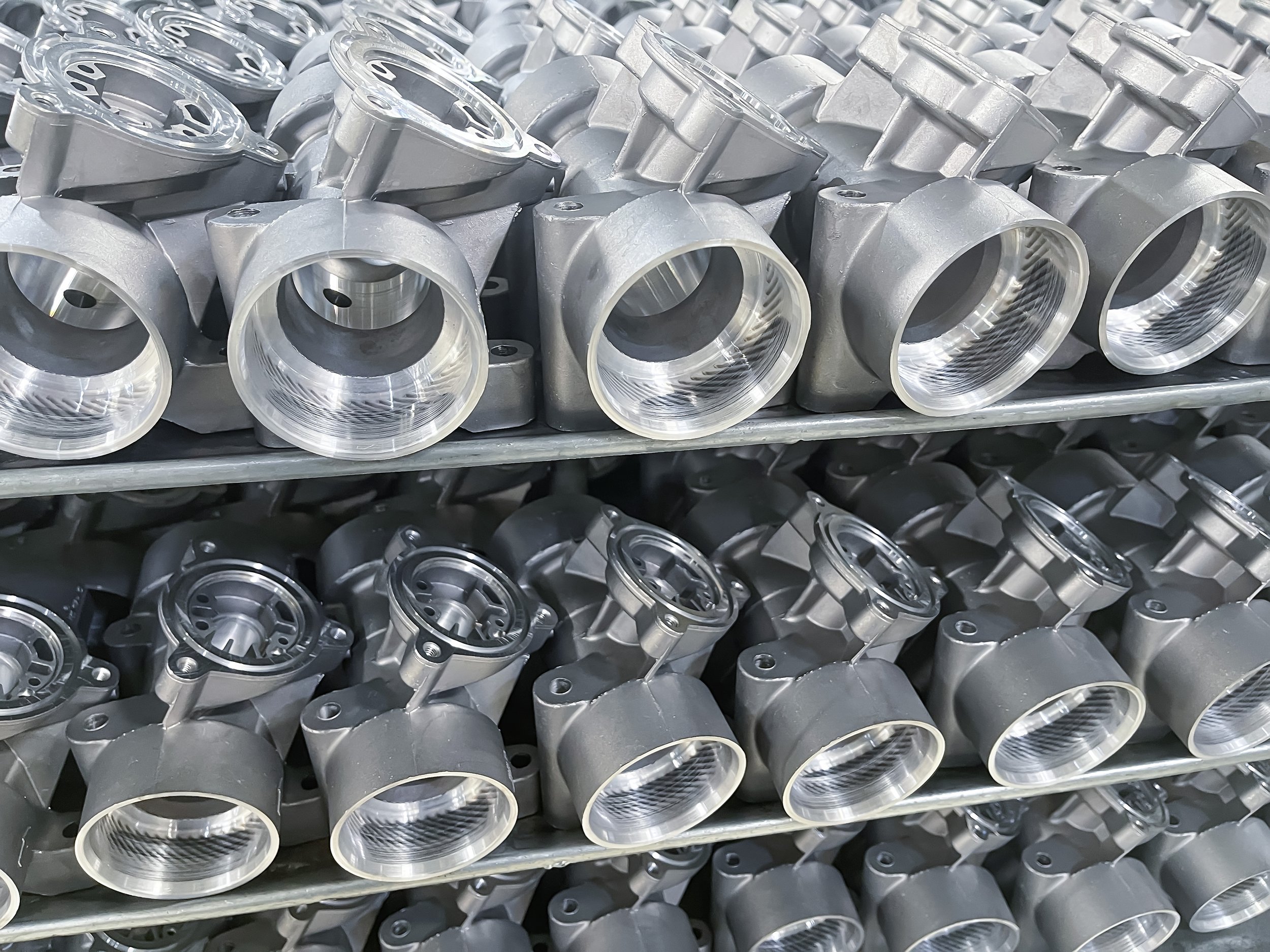
Metal Injection Molding - Wax Removal
Solvent vapor degreasing is an excellent way to remove wax from the cavities of metal injected molded (MIM) parts.
Metal injected molding (MIM) is fast becoming an important part of manufacturing.
One of the most important aspects of metal injection molding (MIM) is "debinding" or "dewaxing" the part once molded. In the past, the debinding or dewaxing process was time consuming and somewhat tedious... but with solvent vapor degreasing, dewaxing becomes fast and easy. Solvent vapor degreasing handily takes the wax into solution and reduces debinding times from hours to minutes.
Metal injection molding uses binders (like wax additives) to hold the metal powder together during the injection molding process. The Metal Injected Molded (MIM) parts, also known as green bodies or green parts need to have the additive waxes removed prior to sintering. Sintering is the process of making (a powdered material) coalesce into a solid or porous mass by heating it. The "green bodies" are heated to harden. However, if the additive waxes are not removed prior to sintering, the entire part could "melt" or collapse in the sintering process; making a mess and causing lost production.
Benefits of Solvent Vapor Degreasing to Dewax
Enter solvent vapor degreasing, which has the two-fold benefit of using solvents that take the wax into solution, and heat to create solvent vapor that penetrates deep within the green part to "pull" the wax out of the deep blind holes and other cavities that are unique to the MIM part.
Solvent vapor degreasing reduces the debinding process time from 100 hours (as used in thermal binder degradation) to minutes.
An additional benefit of solvent vapor degreasing is that the solvents used are non-flammable, fast evaporating, do not leave a residue and are effective...unlike some of the debinding solvents of the past.
Vapor Degreasing Experts™ for the Additive Manufacturing Industry
The Only Company That Manufactures Both Solvents and Equipment for
Complete Cleaning of Molded Parts
Vapor Degreasing Solvent
Advantages of AeroTron-AV Solvent
Cleans titanium, stainless steel and other metals
Enhances ultrasonic cleaning of tiny geometries
Safer for your people and the environment
Ideal nPB and TCE replacement
Effective on a wide variety of soils
Lower cost than other fluorinated based solvents
Strong cleaning performance
Use in your current equipment
Not subject to NESHAP regulations
Vapor Degreasing Equipment
Advantages of the ULTRA™ Vapor Degreasing Equipment
Excellent solvent containment = Reduced solvent cost
NESHAP Compliant
Minimized worker solvent exposure
Automation for part cleaning consistency
Units with immersion, vapor, spray, and ultrasonics – available now
Easy maintenance
Excellent training
The Dewaxing Process
Green bodies are placed in the cleaning basket and lowered into the vapor degreaser.
The MIM parts are heated while the solvent condenses around the entire part and moves into blind-holes and grooves to take the wax into solution (dissolve the wax).
If needed, the MIM parts can be immersed into the boiling solvent for additional wax removal.
After 5-30 minutes (depending on the amount of wax to be removed), the parts are brought to the refrigeration zone - where they are cooled and ready for sintering.
1. Start - green body parts lined up in basket.
2. Parts being put in solvent vapor degreaser.
2b. Parts being heated and exposed to solvent vapor.
3. Parts being immersed in solvent and ultrasonics.
4. Parts being dried in cool zone of unit.
Reliance Specialty Products, Inc.
The Only OEM Company That Manufactures Both Vapor Degreasing Equipment and Vapor Degreasing Solvent
Reliance Specialty Products, Inc. is known throughout the industry as vapor degreasing experts because we manufacture both the ULTRA™ vapor degreasing equipment line and AeroTron™ vapor degreasing solvents which are drop-in TCE and nPB replacement solvents.
ULTRA™ Vapor Degreaser FEATURES:
Minimize worker solvent exposure
Enhance solvent containment
Provide state of the art control systems
Allow easy field maintenance
Automate basket handling for consistent parts processing
Adept for the use of non-flammable solvents