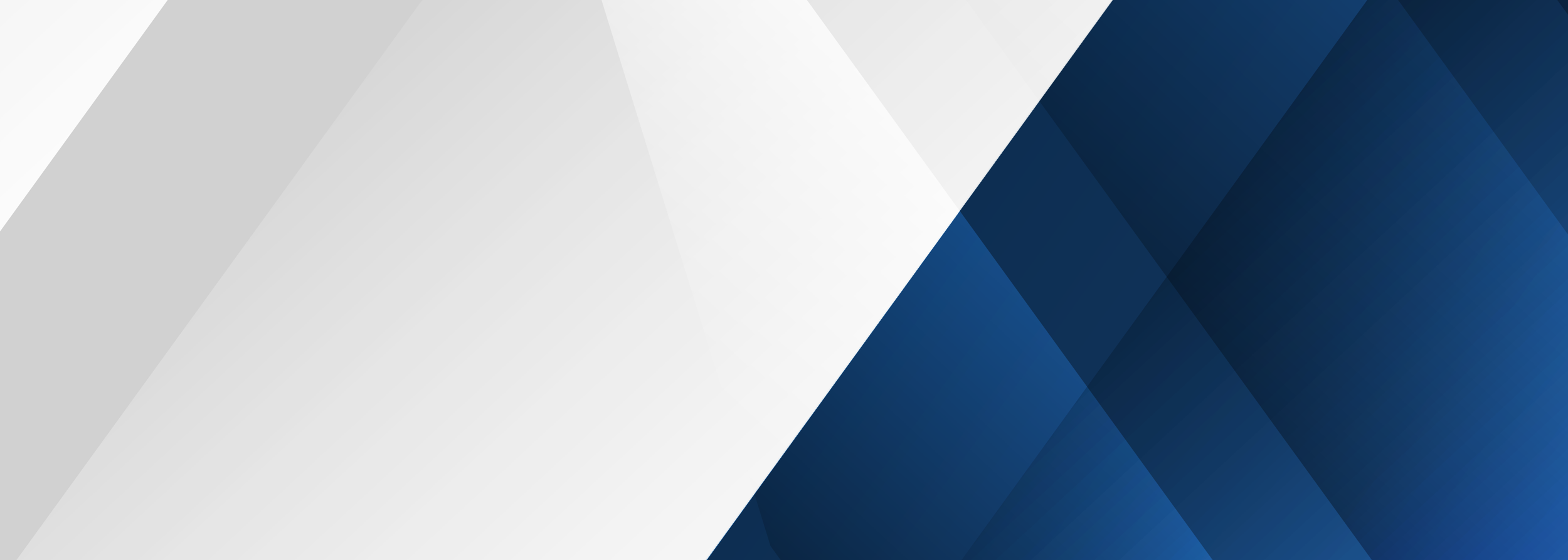
Reliance ULTRA™ Automated Basket Handling System (BHS)
AUTOMATED BASKET HANDLING SYSTEMS
Minimize worker solvent exposure
Save on labor costs
Provide consistency in processing parts
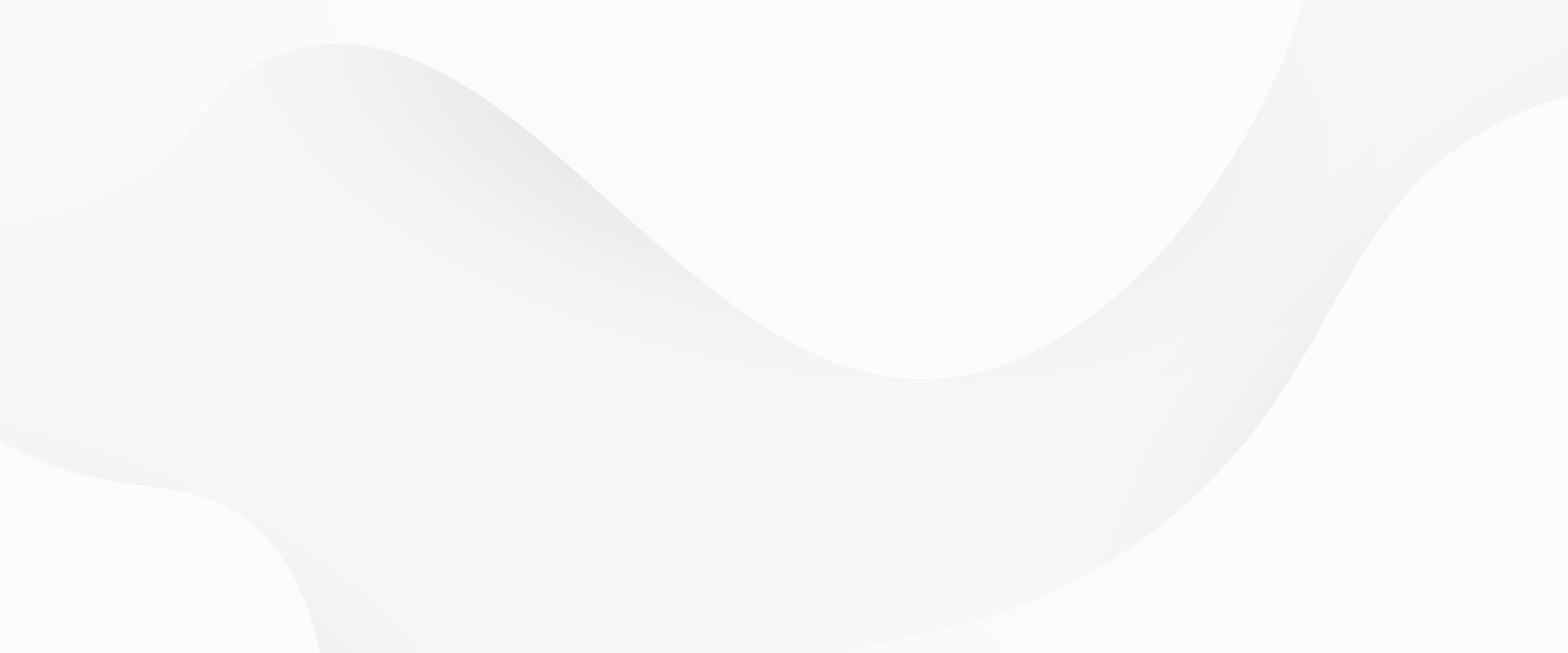
Reliance ULTRA™
Ground Loading Automated Basket Handling System (BHS)
Hoists, Lifts or Basket Handling Systems on vapor degreasers are becoming essential operating equipment and standard operating procedure for many companies. The ability to load parts into a basket and then have the automated system process the parts while allowing the operator to perform other functions reduces cleaning processing errors while increasing productivity and efficiency. Operators can be completing other tasks while the vapor degreaser is processing parts.
Additionally, the hoist allows for more and/or heavy parts to be processed than would otherwise be possible by a single operator. The uniformity of cleaning process and reduced operator error makes hoists (or lifts) an excellent addition to any vapor degreasing system.
WHY WOULD I NEED A LIFT OR A HOIST?
BHS FEATURES
Feature | Description |
Movement | Horizontal Travel over boil sump and ultrasonic immersion sump. Vertical Travel with 5 vertical stop positions on each horizontal axis. Position and length of dwell is PLC controlled. |
Cleaning Recipe Capability | 30 recipes |
Weight Capacity | 100 lbs. including part basket |
Controller | PLC Touchscreen Controlled |
Manual Operation Mode | Allows for manual operation through the PLC touch screen |
Automated Operation Mode | Automatically processes the part basket according to the cleaning recipe selected by operator |
Operator Selection of Cleaning Recipe | System allows for the operator selection between any of the 30 recipes that you created |
Operator Lock-Out of Cleaning Recipe Content | Cleaning recipes are easily stored in a password-protected menu. The operator cannot change the content of a recipe without the password. |
Safety Operating Interlock | Prevents automatic operation if lid is not open, if heat is not operating, if system is not in full vapor reflux, or if there is lift operating system fault |
Emergency Stop Button | At vapor degreaser control panel |
Vapor Containment Enclosure | 3-sided transparent enclosure on horizontal surfaces for reduced vapor zone disturbance and viewing of mechanicals |
Cycle Status Light Pendant | Includes light pendant to advise of the state of the BHS lift including Ready, In Cycle, Cycle Complete and Fault Error |
Lid Closed Basket Processing | Automated horizontal slide lid allows parts basket to be processed through the cleaning cycle with the lid closed for enhanced solvent containment |
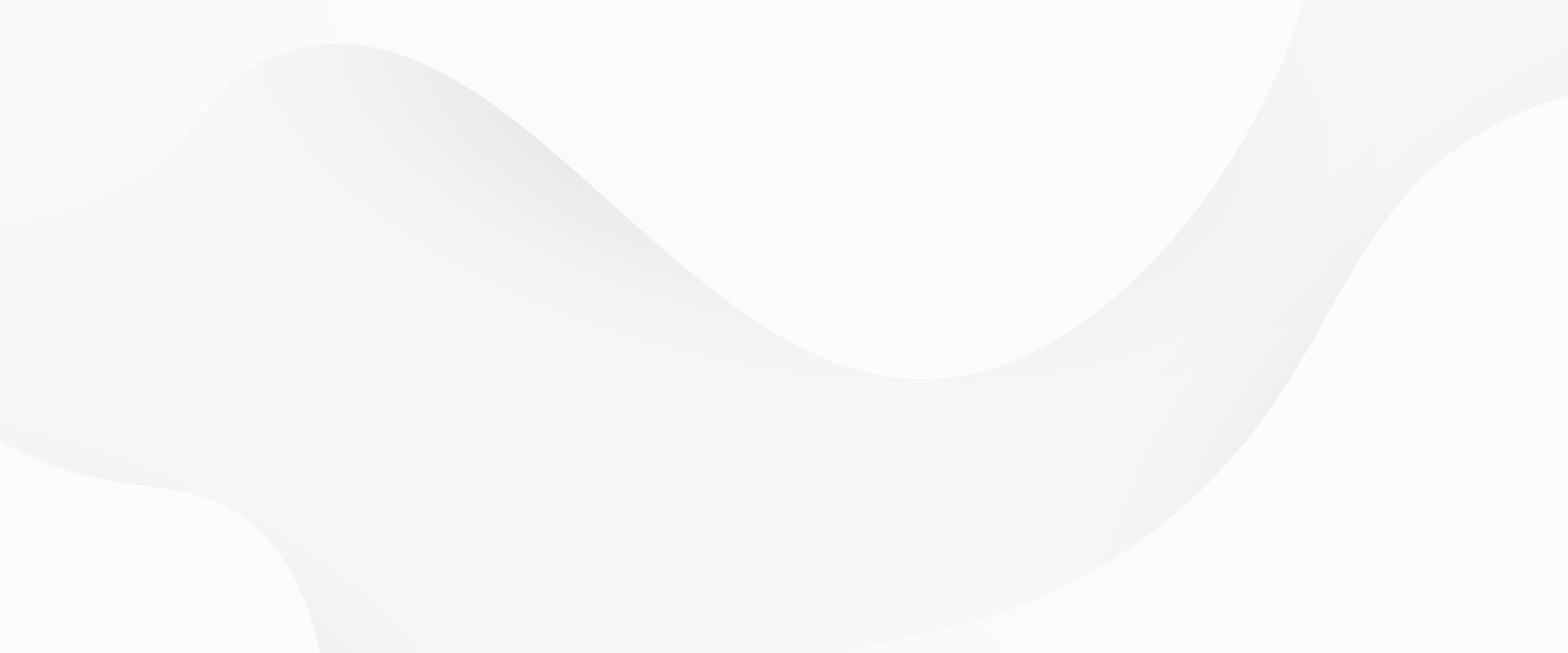
RELIANCE PROGRAMMABLE CONTROL LOGIC (PLC)
AUTOMATED BASKET HANDLING LIFT SYSTEM
FEATURES
NESHAP Compliant - Vapor Degreasing System
Available where the system loads and unloads at the top (top-loading configuration) or the system loads and unloads at ground level (ground-loading configuration)
Several basket weight capacities available: from 75 lbs. (34 Kg) to higher weight capacities of 150 lbs. (68 Kg) - if desired
Light pendant and optional audible signal when the cycle is complete
Automated Horizontal Slide Lid
Emergency stop button
Lift system can be enclosed with clear plastic sheathing
Basket Handling System (BHS) has a Program Logic Control (PLC) touchscreen display:
Simple formatted 6" touchscreen for management to create up to 30 different part-cleaning recipes
Operators can select the part-cleaning recipes created by management but not change them
Programming is password-protected so only management can access and change part-cleaning recipes
Remote access ability to update programs off-site
BENEFITS
NESHAP Compliant features that minimize worker solvent exposure and enhance solvent containment
Save on labor costs as operator not needed to process parts
Consistency in the processing of parts, ensuring each part of cleaned to the same processing specification
Customizable with different part-cleaning recipes for different part-processing. (Example of a part-cleaning recipe: Load; 3 minute vapor dwell; 2 minute ultrasonic immersion; 2 minute vapor dwell; 2 minute refrigeration zone dwell; unload)
Simple Engineering and stoutness of design for durability, field supportability and ease-of-maintenance
Excellent Training for engineering design, start-up, shut down, maintenance and good solvent cleaning work practices
Easy to support in the field with accessible heating elements, replaceable ultrasonics, clear Watlow temperature read-outs, sophisticated indicator light system, simple to trouble-shoot electrical systems and updated refrigeration systems using widely available standard refrigerant
Cost Effective operation and maintenance
Compact footprint
State-of-the-art engineering based on a best current practices amalgamation
Typical Electrical Requirements208V or 230V / 3 Phase, 50/60 Hz.
ULTRA™ GROUND-LEVEL LOAD BASKET HANDLING SYSTEM
ULTRA 2424 w/BHS
ULTRA 2216 w/BHS
THE FUTURE OF AUTOMATED
CRITICAL CLEANING
Configured for load and unload at ground level to the right of the vapor degreaser tank
Automated PLC controlled system
Up to 30 separate part cleaning cycles can be programmed into PLC
Can handle basket loads from 75 lbs to150 lbs
Encoder Locating for precise basket location control
Remote access and programming
State-of-the-art engineering
Available on the ULTRA 2424LE & 2216LE Models
Reliance Specialty Products, Inc.
The Only OEM Company That Manufactures Both
Vapor Degreasing Equipment and Vapor Degreasing Solvent
Reliance Specialty Products, Inc. is known throughout the industry as vapor degreasing experts because we manufacture both the ULTRA™ vapor degreasing equipment line and AeroTron™ vapor degreasing solvents which are drop-in TCE and nPB replacement solvents.
ULTRA™ Vapor Degreaser FEATURES:
Minimize worker solvent exposure
Enhance solvent containment
Provide state of the art control systems
Allow easy field maintenance
Automate basket handling for consistent parts processing
Adept for the use of non-flammable solvents